Centrifugal Pump with Speed Control
- uesuae
- Jul 25, 2020
- 4 min read
Electrical Motor
An electrical motor is a rotating device which converts electrical energy into mechanical energy. It operates through the interaction between the motor's magnetic field and electric current in a wire winding to generate force in the form of torque applied on the motor's shaft.
Rotor has static magnetic fields. Stator obtains current from the drive which sets up a magnetic field. This rotating magnetic field deviates the rotor. Frequency depends on the how regularly the current flows through the stator.

2 pole motor
A 2 pole motor is a type of motor with a pair of magnetic poles. It shows a north-south configuration. It is more efficient with high speed and more RPM. At Hz, a it has 3600 rpm

4 pole motor
A 4 pole motor is a type of motor with two pairs of magnetic poles or 4 magnetic poles with a north-south-north-south configuration. It consumes more energy and fewer RPM and delivers more torque per horsepower and work output. It has a base speed of 1750,1740 or 1725.
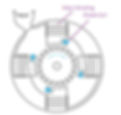
Variable Frequency drive (VFD)-
Variable Frequency Drive is used for running an AC motor at variable speeds or let them ramp up their speed to give them a smooth startup. VFD transform fixed frequency three phase power input to variable frequency three phase output to motor. Usually due to motor constraints frequency is lower or constant as supply.
Centrifugal Pump
A centrifugal pump is a mechanical device designed to move a fluid by means of the transfer of rotational energy from one or more driven rotors, called impellers. Fluid enters the rapidly rotating impeller along its axis and is cast out by centrifugal force along its circumference through the impeller’s vane tips. The action of the impeller increases the fluid’s velocity and pressure and also directs it towards the pump outlet. The pump casing is specially designed to constrict the fluid from the pump inlet, direct it into the impeller and then slow and control the fluid before discharge.
The key component of centrifugal pump is impellers.
Fluid enters the impeller at the eyes i.e. its axis and exits along the circumference between the vanes.
The impeller on the opposite side to the eye is connected through a drive shaft to a motor and rotated at high speed.
The rotational motion of the impeller accelerates the fluid out through the impeller vanes into the pump casing.
To translate the fluid flow into a controlled discharge at pressure, volute pump casing or diffuser pump casting is used.

Conventional way of Flow control
To control the required flow, a control valve is installed and suppressed at pump discharge.

Varying Pump Capacity by throttling

Flow Control using speed control:-
Pump flow rate will get deviated by varying the pump speed using VFD/VSD. Pump will accompany the system resistance curve.
· By transforming pump speed, VFD/VSD supervenes the curve
· VFD / VSD pump employs its unique performance curve shape.
· % change in speed switches same % of flow rate if no static head is accessible
Specifying Speed control pumps
Proper sizing is a crucial factor in case of VS pumps.

Specifying VFD pumps:
NPSHr and Motor HP shall be satisfactory for all flow and head range. NPSHr also hinges on viscosity and its effects shall be substantiated with pump vendor. At lower flow rate customarily HPSHr increases, follows bathtub curve and same shall be substantiated with vendor.
Benefits of variable speed benefits
- Controls speed variations - Provides mechanical control - Eliminates startup impacts causing system vibration - Provides fault tolerance - Supports soft starts - Restarts spinning load - Controls speed swings - Enhances product quality - Can conserve energy in some systems - Improves power factor
Potential issues in Variable Speed Drive
- Fault-out (equipment shut-down) when power quality varies - Harmonics could effect instrumentation - Mechanical vibrations - Increased noise (acoustical) - Static head considerations
- Bearing currents - May need to include a full voltage starter as a bypass control
Impact of VSDs
- High switching frequencies can create additional heating which will lower the efficiency of the motor. - Vibration - Bearing problems: By using insulated bearings or a shaft grounding device we can prevent the pitting of the races. - Cooling air flow reduction: Motor speed should always be greater than the point of compromising fan cooling. - Conductor insulation breakdown: Distance between motor and VSD increases and leads to voltage overshoot and thus motor insulation stress is caused.
- Service factor: By using VSDs many manufacturers started de rate the motor service factor. - Motor Torque: When a constant torque is required, the motor must be sized accordingly at lower speeds.
VSD vs. VFD
Cost effective: VSD is cost effective only up to 80% of speed. VFD becomes only reasonable option as compared to VSD
Bypass: VFD can be by passed if full speed operation is involved, whereas VSD cannot be by passed as it is assigned to machine.
Full speed: VFD can be arranged with a fail-safe peculiarities and pump can run at full speed, however VSD cannot.
Typical capacity control
High pressure control will be discharge pressure control.
Capacity control will be the suction pressure.
Suction pressure/ tank level is maintained through cascade control by adjusting the station capacity by pressure or level influencing the pump speed.
End of curve control
Pumps are designed and selected to operate near their highest efficiency point. If they operate at the right-hand end of the pump curve the likelihood of cavitation increases. The suction and discharge pressures fluctuate wildly pulling and pushing the impeller about because of the out-of-balance forces. The shaft rattles; mechanical seals are damaged; packing is worn; bearings are destroyed by brinelling (hammering) and shafts are bent. Pumps will be noisy, vibrate and shake, get hot and the microjets of liquid ejected by imploding bubbles will hit and erode the impeller metal. Consequently, the pump will fail often and need a lot of maintenance.
The content of this article is taken from web open source. The blogs are intended only to give technical knowledge to young engineers. Any engineering calculators, technical equations and write ups are only for reference and educational purpose.